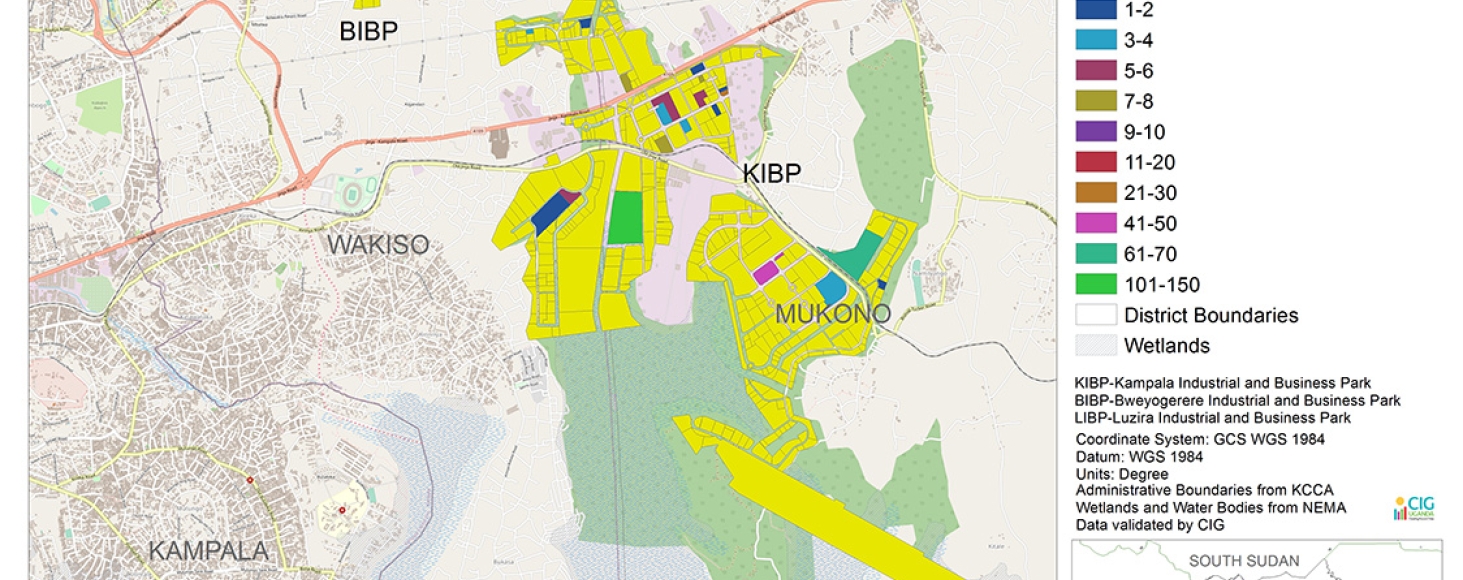
While the Ugandan power sector performance has significantly improved on several metrics since its privatization in the early 2000s, the performance can be described as sub-optimal relative to its full potential. The quality of service has been lagging behind the growth in demand for reliable power, especially from industry. Causes of underperformance are varied and complex and include, but are not limited to, misalignment between investments in Transmission and Distribution (T&D) on one hand and demand by industry on the other; high tariffs and grid growth and connection ambitions that are not matched by planned investments.
Recognizing the symbiotic link between the manufacturing sector and the Energy Supply Industry (ESI), in that a highly productive manufacturing sector is vital to the financial viability of the power sector and vice versa; the Uganda Manufacturers Association (UMA) partnered with ORI (funded under the FCDO funded Cities and Infrastructure for Growth Program) to deliver a manufacturing sector energy demand mapping study. The study focused on manufacturers located in the Greater Kampala Metropolitan Area (GKMA) industrial corridor.